
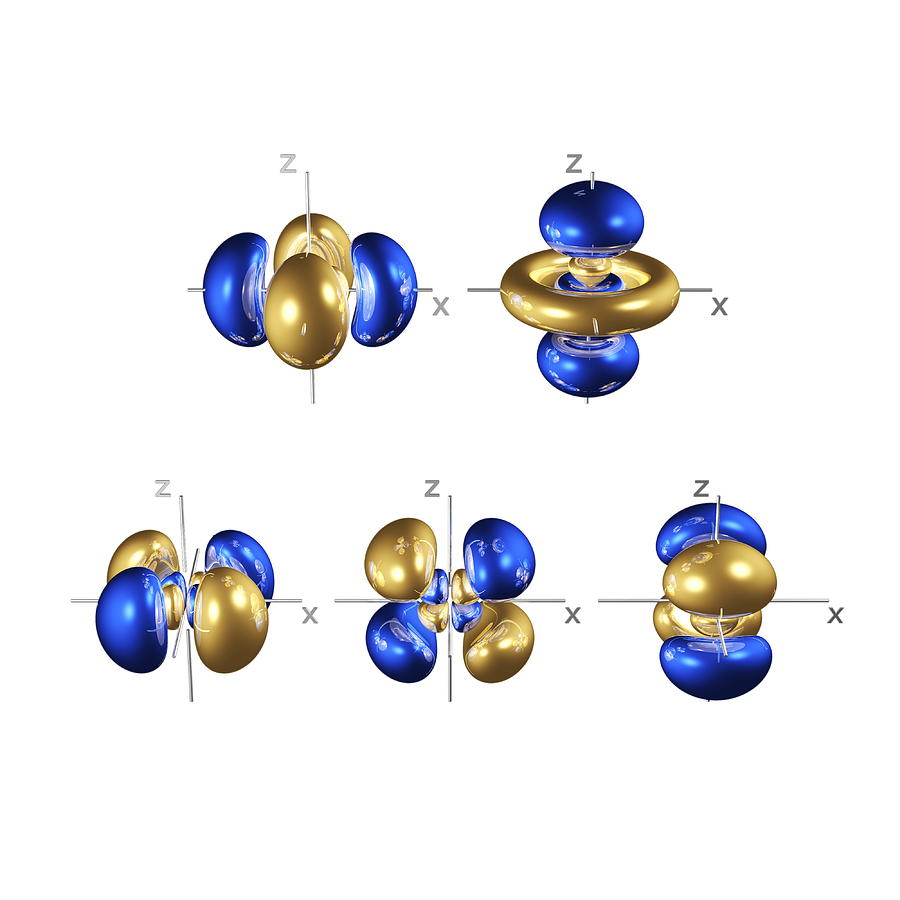
These microfibrils are embedded into a soft acrylamide matrix for structure. Cellulose fibrils combine during the printing process into microfibrils with a high aspect ratio (~100) and an elastic modulus on the scale of 100 GPa. Taking precedent from this, the team developed a composite hydrogel architecture with local anisotropic swelling behavior that mimics the structure of a typical cell wall. Branches, stems, bracts, and flowers respond to environmental stimuli such as humidity, light, and touch by varying the internal turgor of their cell walls and tissue composition. Understanding anisotropic swelling and mapping the alignment of printed fibrils allowed A. This process is reversible, as reverting the temperature and humidity changes caused the sample to unroll again. One ester had a substitution degree of 0.3 (highly hydrophilic) and the other had a substitution degree of 3 (highly hydrophobic.) When the sample was cooled from 50 ☌ to 22 ☌, and the relative humidity increased from 5.9% to 35%, the hydrophobic side contracted and the hydrophilic side swelled, causing the sample to roll up tightly. They developed a bilayer film using cellulose stearoyl esters with different substitution degrees on either side. explored the possibilities of a cellulose-based material that could be responsive to humidity. They produced a chain that would spell "MIT" when submerged in water, and another chain that would morph into a wire frame cube when subjected to the same conditions. The unique properties of these two disparate elements allowed up to 150% swelling of certain parts of the printed chain in water, while the rigid elements set structure and angle constraints for the transformed chain. Skylar Tibbits is the director of the Self-Assembly Lab at MIT, and worked with the Stratasys Materials Group to produce a composite polymer composed of highly hydrophilic elements and non-active, highly rigid elements. The size, shape, modulus, and connection pattern of these material building blocks have a direct relationship to the deformation shape under stimulus activation. Micro scale design is achieved through complex molecular/fiber simulations that approximate the aggregated material properties of all the materials used in the sample. 4D-printed components can be designed on the macro scale as well as the micro scale. Most 4D printing systems utilize a network of fibers that vary in size and material properties. printed, reacting when submerged underwater. Fiber architecture One of the composite polymers that Tibbits et al. Anisotropy is vital in engineering the direction and magnitude of transformations under a given condition, by arranging the micromaterials in a way so that there is an embedded directionality to the finished print.

As opposed to fused-deposition modeling, where the extruded material hardens immediately to form layers, 4D printing is fundamentally based in stereolithography, where in most cases ultraviolet light is used to cure the layered materials after the printing process has completed. Stereolithography is a 3D-printing technique that uses photopolymerization to bind substrate that has been laid layer upon layer, creating a polymeric network. It is therefore a type of programmable matter, wherein after the fabrication process, the printed product reacts with parameters within the environment (humidity, temperature, voltage, etc.) and changes its form accordingly. However, in 4D printing, the resulting 3D shape is able to morph into different forms in response to environmental stimulus, with the 4th dimension being the time-dependent shape change after the printing. 4-dimensional printing ( 4D printing also known as 4D bioprinting, active origami, or shape-morphing systems) uses the same techniques of 3D printing through computer-programmed deposition of material in successive layers to create a three-dimensional object.
